Drawdown Testing: Overview
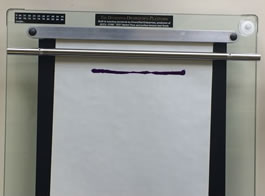
The drawdown test is a fundamental laboratory technique which is used to evaluate interactions between flat surfaces (such as film, foil, and paper) and a myriad of inks, coatings, paints, suspensions, adhesives, colloids, powders, etc.
Since most coating properties are thickness-dependent, it is imperative that the optimum thickness be determined for each application. Drawdowns allow easy evaluation of wettability, opacity, color match, gloss, tack strength, drying weight, dye uniformity, degree of pigment dispersion, and other attributes. For best results, tests should be performed on a Diversified Drawdown Platform™ or a similar flat surface.
The tools described in this section open up a variety of test options. Even when the drawdown method does not directly emulate a planned production process, it may be a useful pre-production test to screen materials or drying and curing methods.
The following table shows the wet film thicknesses, coverage, and wet film weights that can be produced with our stock metering rods and ACCU COAT Applicators™. Additionally, many alternative coating thicknesses can be produced with special order metering rods. A Universal Blade Applicator can produce any wet film thickness from 0 to 5 mils or 0 to 25 mils, depending on the design chosen and how it is adjusted. Please email or call us for advice on your specific application.
WFT, mils(1) |
WFT, microns(1) |
ft2/gal | m2/l | pounds/1000 ft2 | g/m2 | Tool(s)(2) |
---|---|---|---|---|---|---|
0.15 | 3.81 | 10,700 | 263 | 0.78 | 3.81 | A |
0.30 | 7.62 | 5,350 | 132 | 1.56 | 7.62 | A |
0.40 | 10.2 | 4,010 | 98.6 | 2.08 | 10.2 | A |
0.50 | 12.7 | 3,210 | 78.9 | 2.60 | 12.7 | A, B |
0.60 | 15.2 | 2,680 | 65.8 | 3.12 | 15.2 | A |
0.70 | 17.8 | 2,290 | 56.4 | 3.64 | 17.8 | A |
0.80 | 20.3 | 2,010 | 49.3 | 4.16 | 20.3 | A |
0.90 | 22.9 | 1,780 | 43.8 | 4.68 | 22.9 | A |
1.0 | 25.4 | 1,610 | 39.5 | 5.20 | 25.4 | A, B |
1.2 | 30.5 | 1,340 | 32.9 | 6.24 | 30.5 | A |
1.5 | 38.1 | 1,070 | 26.3 | 7.80 | 38.1 | A, B |
1.8 | 45.7 | 892 | 21.9 | 9.36 | 45.7 | A |
2.0 | 50.8 | 803 | 19.7 | 10.4 | 50.8 | A, B |
2.2 | 55.9 | 730 | 17.9 | 11.4 | 55.9 | A |
2.4 | 61.0 | 669 | 16.4 | 12.5 | 61.0 | A |
2.5 | 63.5 | 642 | 15.8 | 13.0 | 63.5 | B |
3.0 | 76.2 | 535 | 13.2 | 15.6 | 76.2 | A, B |
3.6 | 91.4 | 446 | 11.0 | 18.7 | 91.4 | A |
3.8 | 96.5 | 422 | 10.4 | 19.8 | 96.5 | B |
4.0 | 102 | 401 | 9.86 | 20.8 | 102 | B |
4.2 | 107 | 382 | 9.39 | 21.8 | 107 | A, B |
4.6 | 117 | 349 | 8.58 | 23.9 | 117 | B |
5.0 | 127 | 321 | 7.89 | 26.0 | 127 | A, B |
6.0 | 152 | 268 | 6.58 | 31.2 | 152 | B |
8.0 | 203 | 201 | 4.93 | 41.6 | 203 | A, B |
9.0 | 229 | 178 | 4.38 | 46.8 | 229 | B |
10.0 | 254 | 161 | 3.95 | 52.0 | 254 | A |
12.0 | 305 | 134 | 3.29 | 62.4 | 305 | B |
Coating weights are based on a coating density of 1 g/cm3 (8.345 lb/gal). To determine dry film weight, multiply table values by percent solids.
(1) Wet film thicknesses are approximate, and will vary slightly depending on coating viscosity, percent solids, and substrate absorptiveness.
(2) A = appropriately sized metering rod; B = appropriately sized ACCU DYNE ApplicatorTM, held at a 45° angle, which applies the maximum possible yield for each coating gate. Holding these applicators at a lower angle will reduce coating thickness down to about half of the maximum value.